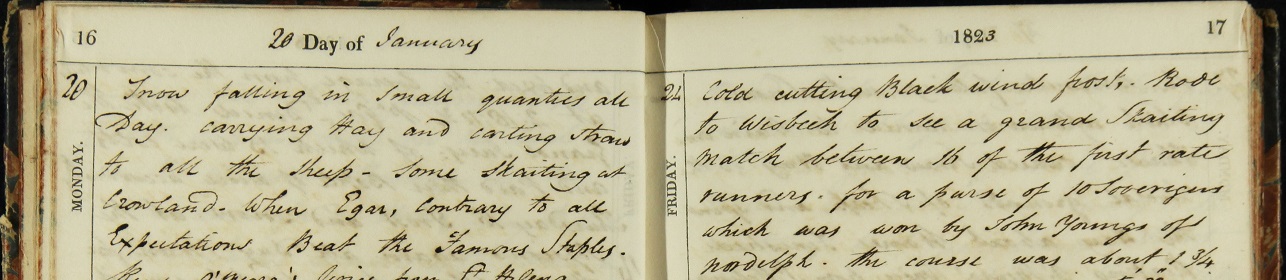
Back to Blogs
16 May 2023
Museum's Urnes Style Brooch recreated by Maria Holzleitner
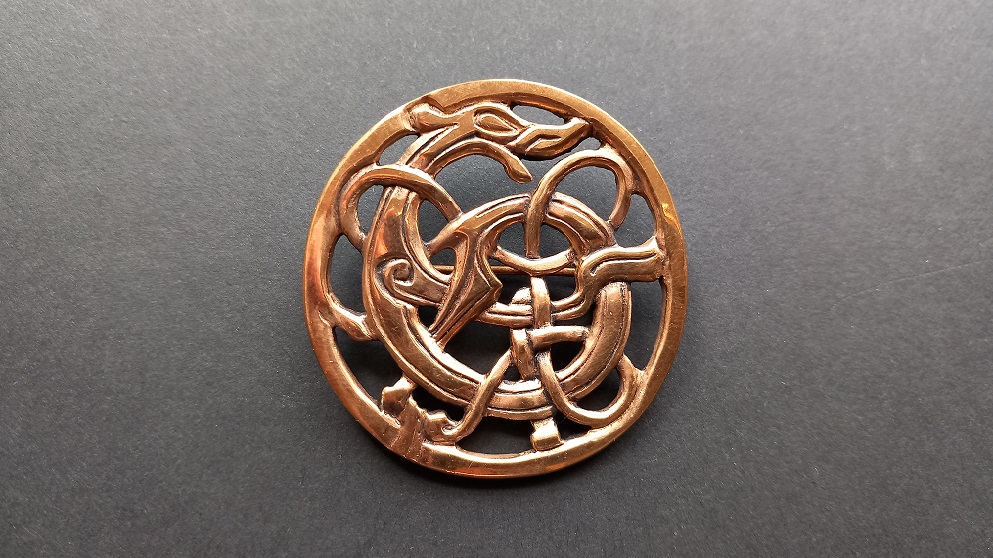
Maria Holzleitner shares with us her process of recreating an Urnes style brooch using an original 11th century brooch from our collection as reference. In 1846 Mr Rumball donated the brooch, which had been found during the construcion of the museum that year.
When recreating historic jewellery I try to use a process that is as close or similar to the process in which the original piece was made.
Of course I have some machines and materials available today, that make the work a lot easier and less time consuming, but the principles remain the same and every piece is crafted by hand.
For the Urnes Style Brooch, I therefore used a lost wax casting method, which I carried out in the following steps.
First I carefully inspect the original piece, either through photographs (which the Wisbech and Fenland Museum was so kind to send me) or I go and look at the original artefact in person, if I get the chance.
With these references I then make a sketch/drawing of the original design, which I need to translate onto wax, and also to actually understand all the things that are going on on the historic object.
I then transfer the drawing onto wax and carve out the piece by hand, as true to the original as I can. Sometimes it needs a second try until I get it right, but it´s all a learning process.
When the wax model is finished, I make a silicon mould of it, which I can use to make more wax models (so I don´t have to carve every single brooch) .
Then brooch fastenings are added to the back of the wax models, they are arranged and put into a metal flask and covered in gypsum to make a mould for the metal casting . In the times, which the Urnes Style brooch originated from, clay was mostly used to form the mould.
Once the gypsum is hardened, the whole gypsum mould is heated, until all the wax inside is evapourated (which takes up to 10 hours) and which leaves a negative form of the brooch behind for the metal.
For the Urnes Style brooch I then melted bronze and cast it into the still heated gypsum mould with the help of a vacuum. Traditionally air canals were carved into the moulds to let the air escape when casting the metal, todaya vacuum helps to skip the step of making air canals.
Lastly I separated the different pieces from the 'casting tree', finished them up, polished them and finally added a needle on the back of the brooches.
To see and find out more about Maria's work visit her on Instagram @ivaldislegacy
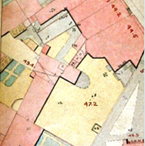
Supporting the museum
To maintain and grow our collections we need your contributions, please support us by donating today.
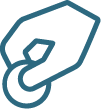